How to save fuel with Indeco HP Fuel Saving hammers
Indeco HP Fuel Saving hammers guarantee fuel savings, efficient demolition and maximum productivity compared to competitors in the same class.
Power in demolition is crucial. But it’s certainly not the only determining factor in assessing the cost-effectiveness of a tool like the demolition hammer. Hence, Indeco now offers the HP Fuel Saving, a hydraulic hammer able to guarantee fuel savings of up to 20% compared to models of equivalent weight and performance produced by other manufacturers. And that’s not all: the Indeco HP series combines Fuel Saving with optimum performance, and Fuel Saving with maximum productivity thanks to its upgraded hydraulic system, allowing better efficiency and improved operating pressure, making best use of the hydraulic power and considerably reducing the engine speed of the operating machine. This becomes even more evident when comparing the Indeco hammer to competing gas- or gas/oil-powered products of similar size. This is an important advantage, not only in terms of environmental protection but also the profitability of the work itself, which increases more than proportionally to the size of the hammer used.
Let’s take a look at the ratio of installed power to fuel consumption:
- The excavator engine provides the hydraulic power in input to the hammer (KW)
- The hammer’s productivity (Pr) is expressed in tonnes/day of crushed rock
- The input power (IP) expressed in KW is given by the oil flow in input (Qi) expressed in l/min multiplied by the breaker pressure in input (Pi) expressed in bar, /600
- The demolition power (OP) in output (KW) is equal to the energy per blow (J) multiplied by the number of blows per minute (BPM) and the internal efficiency of the breaker (higher efficiency for oil-powered hammers and lower for gas- or gas/oil-powered hammers)
- The lost power in output (LP) in KW, that is, the excavator’s hydraulic power which is not converted into mechanical energy by the breaker (and therefore into productivity Pr ton/day), but which is discharged directly into the tank, is given by the oil flow rate in output (Qe) in l/min, multiplied by the back pressure in output from the breaker (Pe) in bar / 600
- Since the oil flow rate is equal in input and in output (QI = QE), the lost power (LP) will be directly proportional to the value of the oil back pressure returning to the excavator tank
- The less the back pressure in output, the more efficient the demolition hammer
- To achieve the same productivity in the presence of high back pressure, the power in input must therefore be significantly increased, and thus consume more fuel
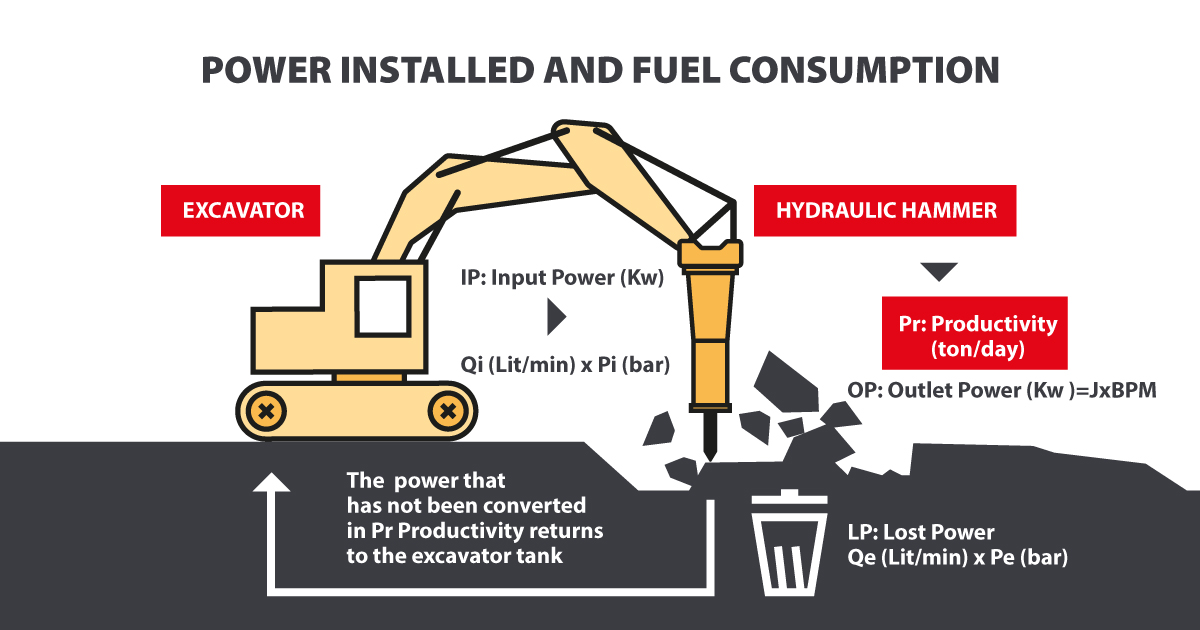
What makes Indeco demolition hammers “Fuel Saving” with maximum productivity?
- Only one moving part, the distributor, aligned with the piston
- High hydraulic efficiency of the internal oil distribution, which is free of grooves and without a long internal channel, change of direction or reduction in diameter
- A single oil seal between the cylinder and blowback piston, which means low friction
- No gas seal on the top part of the piston (low friction and high reliability)
- Seal-free nitrogen accumulator, separate to the piston, leak-free
- The patented automatic blow speed-energy variation, depending on the hardness of the rock, which ensures the right impact energy is always used for maximum productivity
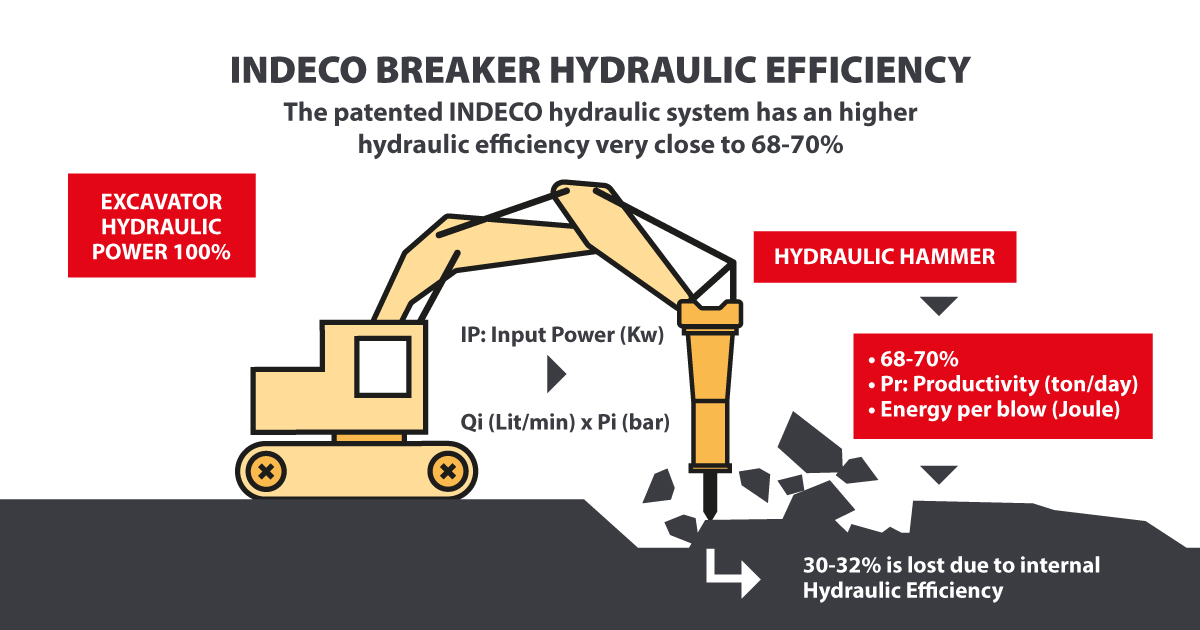
What causes low efficiency in gas-powered hammers?
- A distributor split in two or more parts and far from the blowback piston
- Lots of grooves, long internal channels, lots of changes in direction and diameter reductions
- Two or more oil seals on the cylinder, which means high friction
- Two or more gas seals on the top part of the piston (high friction and low reliability)
- Leaks from the nitrogen accumulator caused by the seals and piston movements
- High discharge back pressure, necessary to operate gas-powered breakers, but which increases the power lost during operation
- Due to the high discharge back pressure and low internal efficiency (complex internal distribution and high number of seals), gas- and gas/oil-powered breakers require high oil flow rates and high operating pressure to function, thus increasing the excavator’s fuel consumption by up to +20% compared to oil-powered breakers in the same class
- The fixed blow, which, rather than adapt to the hardness of the rock, keeps the hammer set in the maximum energy configuration, preventing optimum productivity from being achieved (often even -50% lower), while also increasing the stress on the hammer’s main mechanical components
How much do fuel savings affect the cost-effectiveness of the demolition hammer?
In comparing the actual operating data of the largest demolition hammer, the Indeco HP 18000, and another gas-powered version in the same class, it is found that the former requires 18.3% less energy to achieve the same results in terms of productivity, compared with the latter. This translates into a saving of 22,200 litres of fuel per year.
The importance of efficiency in a demolition hammer
- A productive hammer needs to be maintained, following a strict maintenance schedule
- A quality, well-maintained hammer can work well for years on end
- Being able to estimate the spare parts needed is key to ensuring continuity of production and avoiding downtime
- Particularly large companies need to know their running costs (maintenance program)
- The running costs/year of the hammer can be estimated at 15% of its purchase value
- The running costs/year of the excavator can be estimated at 5% of its purchase value
- The cost/year of excavator FUEL is up to 10 TIMES the cost/year of maintaining the hammer (including tools)
- Hammer efficiency is the best compromise between productivity/reliability/costs
- A large hammer can do an excellent JOB even if mounted on an outdated machine, it is difficult to assume otherwise
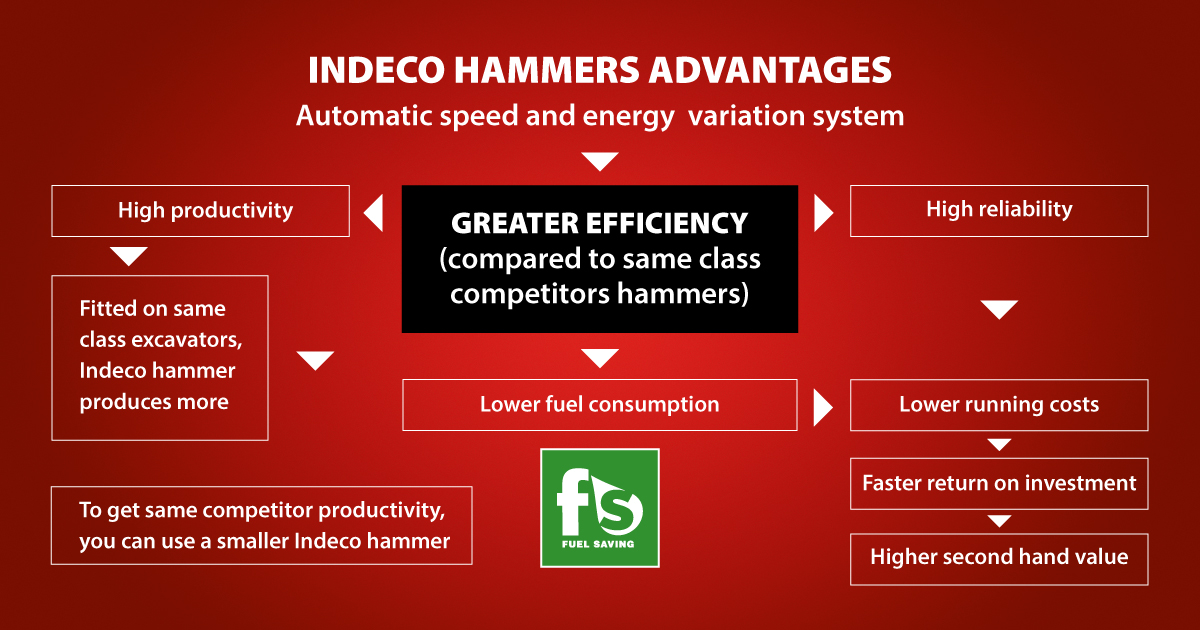